The Search for a New Product Feature
You’ve got a fantastic product on the market, but you want to make it more feature packed. You stumble upon antimicrobial technology, but you’re not entirely sure what it is or how it’s added to a product. You scour the internet, coming across various companies who claim to be experts in the field of antimicrobials. After hours of research, you sit there scratching your head, wondering if this journey is worth the investment.
Sound familiar? You’re not alone!
What is Antimicrobial Product Protection?
In simple terms, antimicrobial product protection is an invisible feature that gives products a built-in resistance to microbial growth. The technology is typically added during the manufacturing process and is proven effective against bacteria, mould and mildew. The benefits of antimicrobial protection include an inherently cleaner, fresher, and more durable product.
For over 35 years, Microban International has worked with brands, manufacturers, and product innovators like you to create premium antimicrobial products. Every journey begins with complete transparency, as we guide you through each stage of the product development process.
One of the most crucial steps is correctly mixing the antimicrobial agent into your material type.
Which Mixing Method is Right for Your Product?
Making a treated product is like baking a cake: first you assemble the ingredients, then you weigh them out into set proportions, and then you mix them. However, as with baking a cake, if you don’t get the recipe right then the desired product will not materialise.
Mixing can take on many forms, depending on the type of antimicrobial you are using, the end-product, and your production process. Each form has its benefits, but the intensity and level of mixing is key to creating an antimicrobial-treated product that performs.
Typical Examples of Mixing
- Powder Blending: Typically, low shear / low to medium speed blending is more than enough to mix a powder to powder blend. Residence time in the blender to evenly distribute the “additive” is a key factor to a good mix. Mixing powders into liquid formulations requires high speed / high shear to ensure thorough dispersion and distribution prior to use. Powder blending is often used for treating cement-based grout applications. For example, Building Adhesives Ltd (BAL) integrate a powder formulation to produce an antifungal tile grout that is resistant to mould growth.
- Liquid Blending: Once material compatibility has been satisfied, high speed and high shear blending is essential in liquid mixing to ensure a homogenous blend. Density / viscosity of the materials being mixed also has an important role to play. TOA Paint (Thailand) use a liquid antimicrobial agent to maintain the dry film preservation of their interior paints against bacterial and fungal spoilage.
- Pellet Mixing: The ideal method of handling thermoplastic pellet mixing is to use dedicated loss in weight or volumetric feeder, although basic methods of mixing (tumble, Z blade) can also provide adequate distribution of the antimicrobial additive. The real mixing takes place in the “melt” cycle of the process, be it injection moulding or extrusion processes. It is important to give yourself the best start by mixing the pellets adequately. Many companies mix pellets for thermoplastic processes with moulding and extruded products. Examples include chopping boards, hatchery baskets, shower curtains, food containers, and cladding panels. Star Industrial (chopping boards), Adamo Srl (plastic kitchenware), Nanny (baby products), and Speck Products(cell phone cases) are all Microban partners who each utilise thermoplastic pellet masterbatches to enhance the features and functionality of their products.
And We All Mixed Happily Ever After...
In all mixing situations it is important not to overfill the mixer, leaving adequate room for material to “move” around. This helps disperse and distribute the antimicrobial throughout the material being treated.
It’s also essential you partner with a company that understands the many nuances of antimicrobial technology and how it should be added to a product. This will help you to avoid spending time developing a product that doesn’t perform as expected.
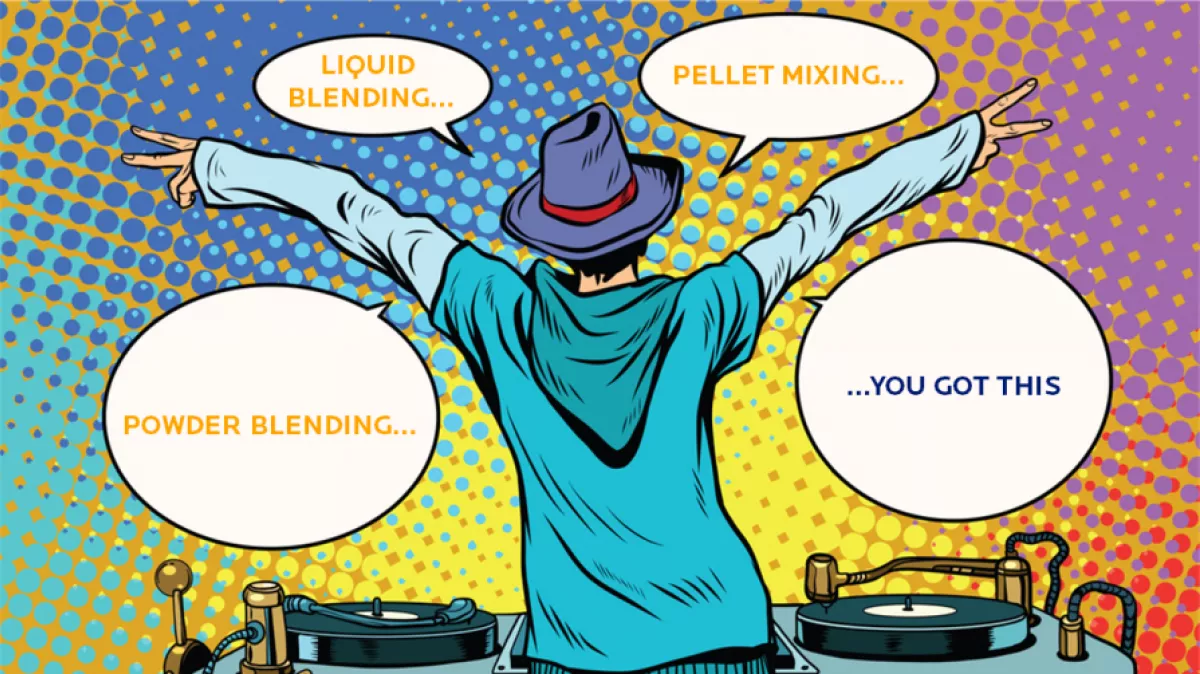
Microban’s team of technical specialists can quickly tune in to your product requirements. Decades of experience means we can identify the right antimicrobial solution for your material type, and we will help you to seamlessly incorporate this into your product.
Microban® antimicrobial technologies are available in powder, liquid and thermoplastic pellets. Each formulation has undergone extensive independent laboratory testing and has a long history of safe use.
For more information about adding an antimicrobial feature to your product, contact a member of the team today.